SCHIENEN-DIENSTLEISTUNGEN
Dank langjähriger Investitionen verfügen wir über einen modernen Maschinenpark und können Schienen von höchster Qualität für berührungslose Hochgeschwindigkeitsstrecken anbieten. Das fertige Produkt ist maximal 360 m lang und wird von uns an den Einbauort geliefert.
Der angebotene Prozess ist automatisiert und computergesteuert und sorgt für ein Endergebnis, dass den Effekt vom Thermit-Schweißverfahren deutlich übertrifft.
ABBRENNSTUMPFSCHWEISSEN VON SCHIENEN
Die modernste Schienenschweißanlage Polens ermöglicht die Lieferung von Schienen mit einer maximalen Länge von 360 m, die aus Abschnitten von 30 m bis 120 m hergestellt werden. Ein spezieller Maschinenpark ermöglicht die Lieferung von Schienen, die die Anforderungen der EN 14587-1 von 2019 und der Technischen Bedingungen Id-112 vom 12.11.2013 erfüllen.
Sehen Sie, wie das Schienenschweißverfahren abläuft:
-
Zuführung der Schienen zum Beschickungstisch
Die auf Eisenbahnwagen angelieferten Schienen werden auf unserem Lagerplatz entladen und dann auf den Beschickungstisch geladen. Das Ent- und Beladen erfolgt mit Spezialkranen, die mit Traversen und Dauerelektromagneten ausgestattet sind.
-
Transport der Schienen in die Schweißanlage
Die eingelagerten Schienen werden mittels eines Zuführwagens automatisch vom Beschickungstisch entnommen und mit einem Rollenförderer mit Elektroantrieb in die Halle transportiert, in der der eigentliche Schweißvorgang stattfindet.
-
Erhitzen von Schienen
Der Rollenförderer mit Elektroantrieb, mit dem die Schiene in die Schweißanlage transportiert wird, ist mit einem automatischen System zum Erhitzen von Schienenenden ausgestattet, das zum Einsatz kommt, wenn die Temperatur der zu schweißenden Schienen unter 50°C fällt.
-
Reinigung der Kontaktflächen
Die Schienenköpfe und -füße sowie -stirnflächen werden mit einer automatischen Bürstenmaschine gereinigt, um Oberflächenverschmutzungen zu entfernen. Diese Tätigkeit ist sehr wichtig für den korrekten Kontakt von Elektrode zu Schiene und Schienenkopf zu Schienenkopf.
-
Abbrennstumpfschweißen
Die gereinigten Schienen werden in die Schweißanlage transportiert, wo der automatische Schweißprozess startet. Zuerst werden die Schienen zentriert, so dass sie korrekt zueinander ausgerichtet sind, um eventuelle Höhenunterschiede der Schienen auf den Fuß zu übertragen. Nach der Zentrierung erfolgt der kontinuierliche Schweißprozess in folgenden Schritten:
- Plasma-Vorreinigung - Oxide werden entfernt und Schienenstirnflächen ausgerichtet,
- Erhitzen - Schienenenden werden auf die erforderliche Tiefe erwärmt,
- Plasma-Reinigung - Schienenoberflächen werden von den entstandenen Oxiden gereinigt,
- Stauchen - erwärmte Schienenenden werden sehr schnell aneinander gepresst und über eine bestimmte Zeit mit entsprechender Druckkraft zusammen gehalten, um eine Verbindung herzustellen,
- Abscheren - der beim Stauchen entstandene Materialüberstand wird auf die entsprechende Höhe abgearbeitet.
Die Parameter des Schweißprozesses werden automatisch aufgezeichnet und vom Bediener der Schweißanlage laufend überwacht. Der gesamte Schweißprozess wird in Diagrammform dargestellt und kann jederzeit ausgedruckt und dem Kunden vorgelegt werden. -
Kennzeichnung
Jede geschweißte „lange“ Schiene erhält eine individuelle Nummer, die mit einem pneumatischen Markiergerät auf den Schienensteg angebracht wird. Darüber hinaus ist jede Schweißnaht mit einer entsprechenden Nummer gekennzeichnet. Die eingeprägten Nummern ermöglichen eine vollständige Rückverfolgbarkeit der Schweißnaht sowie der gesamten Schiene.
-
Abkühlung von Schweißnähten
Die geschweißten und markierten Schienen werden mit dem Rollenförderer mit Elektroantrieb zu einem Zwischengerüst transportiert, um die Schweißnähte auf die entsprechende Temperatur abzukühlen.
-
Richten und Schleifen
- Messen und Vorrichten
Die geschweißte Schiene mit abgekühlten Schweißnähten wird einem Bearbeitungszentrum bestehend aus einer Presse, einer Schleifmaschine und einem Lasermesssystem zugeführt.
Im ersten Schritt wird die Schiene mit drei Laserköpfen auf Geradheit geprüft, um festzustellen, ob sie sich während des Schweißens in keiner Achse verbogen hat. Das Messergebnis wird als Diagramm auf dem Bildschirm angezeigt. Anhand dieses Diagramms wird die Geradheit bei Bedarf mit Presszylindern durch den Maschinenführer korrigiert. Die Mess- und Richtvorgänge werden so lange wiederholt, bis die Geradheit der Schiene im Bereich der Schweißnaht die entsprechenden Geradheitsparameter erreicht.
- Schleifen
Die so vorbereitete Schweißnaht wird dann zur Schleifstation gebracht, wo die Schiene im Bereich der Schweißnaht unter Beibehaltung des Schienenprofils maschinell geschliffen wird.
- Messen, finales Richten
Nach erfolgtem Schleifen der Schweißnaht wird die Schiene in die Pressstation mit dem Messsystem zurückgebracht. Es erfolgt eine weitere Messung der Geradheit, die gegebenenfalls durch die Presszylinder so korrigiert wird, dass die Geradheit im Bereich der Schweißnaht innerhalb des vorgegebenen Maßbereichs liegt.
Das Ergebnis der Geradheitsmessung wird als Diagramm auf dem Rechner gespeichert und kann jederzeit ausgedruckt werden. -
Lagerung von geschweißten Schienen
Die geschliffenen und gerichteten Schienen werden mit dem Rollenförderer mit Elektroantrieb aus dem Bearbeitungszentrum abtransportiert und mittels eines Zuführwagens auf einem Gerüst abgelegt. Anschließend werden sie mit Hilfe von Hebezeugen, die mit Traversen und Dauerelektromagneten ausgestattet sind, auf das Lagerplatz gebracht, wo sie gestapelt gelagert werden. Mit denselben Hebezeugen können die Schienen für den Transport zur Baustelle auf spezielle Wagen verladen werden. Die Entladung erfolgt mit einem speziellen Entladewagen, der von unserem Personal bedient wird.
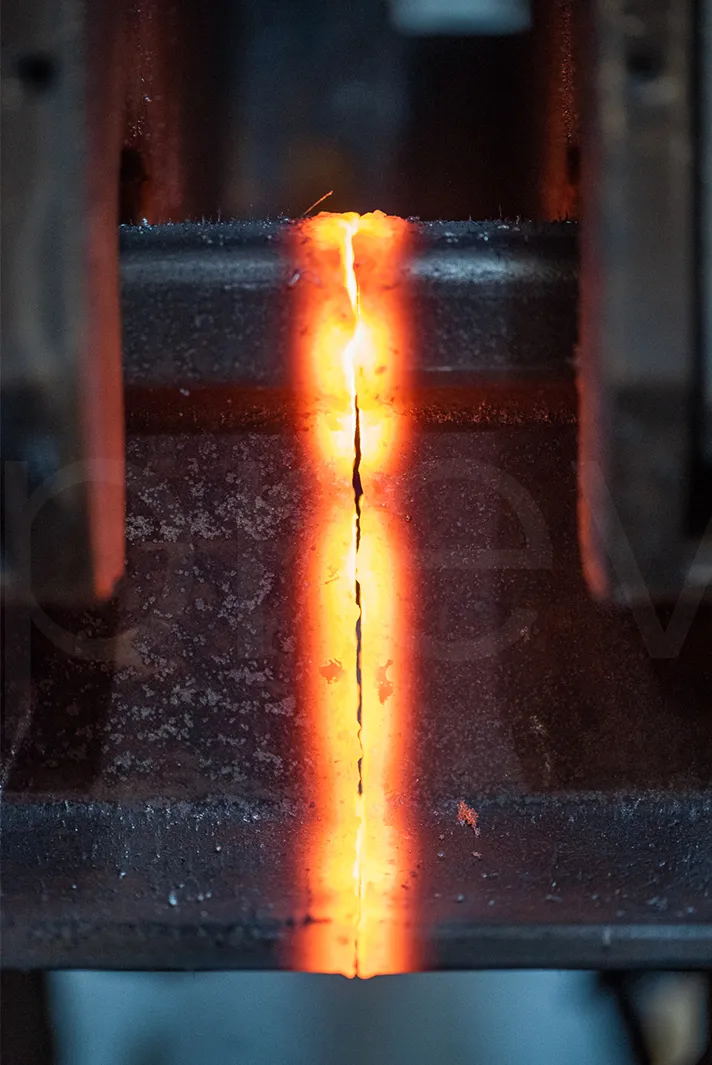
Siehe Prozessdetails
-
Reinigung der Schiene
Sowohl der Kopf als auch die Stirnseite der Schiene werden von Rost und Schmutz befreit, um einen optimalen Kontakt mit den Elektroden zu gewährleisten. -
Plasma-Reinigung
Kontaktflächen werden erhitzt und Restverschmutzungen entfernt. -
Stauchen
Die Schienen werden mit großer Kraft gepresst, was die Einhaltung der Anforderungen ID112 und PN EN 14587-1 für Schienenschweißungen gewährleistet. -
Abscheren
Der Materialüberstand wird an die Schienenkontur abgearbeitet.
-
Messen und Richten
Die abgekühlte Schiene wird mit drei Laserköpfen zweidimensional auf Geradheit geprüft. Der Rechner berechnet dann die Druckkraft und den Druckpunkt, um Abweichungen von der Norm zu korrigieren. -
Schleifen
Der Schienenkopf wird von der Seite und von oben maschinell geschliffen, um die gewünschte Krümmung zu gewähren. -
Schleifeffekt
Schiene mit einer glatten Oberfläche für Hochgeschwindigkeitszüge. -
Lagerung
Schienen werden mit einem pneumatischen Markiergerät gekennzeichnet und mit einem Aufkleber mit Identifikationsangaben versehen.
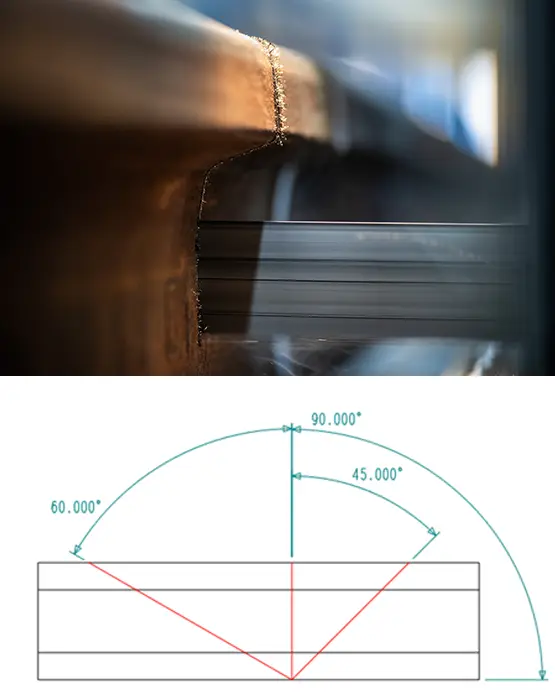
Schneiden von Schienen
Für Schienenprofile: 49E1, 60E1, 54E1, 54E4, 115RE bieten wir das Schneiden von Ausgangsmaterial mit einer maximalen Länge von 120 lm auf die vom Kunden gewünschte Länge (maximal 32 m) mit folgenden Schnitttoleranzen an:
- ≤ 24 m - ± 3 mm
- > 24m ≤ 32 m - ± 4 mm
Rechtwinkligkeit der Schienenenden 0,6 mm in jeder Richtung.
Schneiden von Schienen in Winkel - siehe Zeichnung links.
Schienenbohrungen
Für die oben genannten Schienen bieten wir auch Bohrungen von Schienenstegen im Bereich von Ø 8 mm bis Ø 33 mm an.
Toleranz der Lochposition ± 0,5 mm in jeder Richtung.
Für Weichenzungenprofile 60E1A6, 60E1A1, 49E1A3 bieten wir, ähnlich wie bei Schienen, das Schneiden von Ausgangsmaterial mit einer maximalen Länge von 120 lm auf die vom Kunden gewünschte Länge (maximal 32 m) mit folgenden Schnitttoleranzen an:
- ≤ 24 m - ± 6 mm
- > 24 m ≤ 32 m - ± 10 mm
Rechtwinkligkeit der Schienenenden 0,6 mm in jeder Richtung.
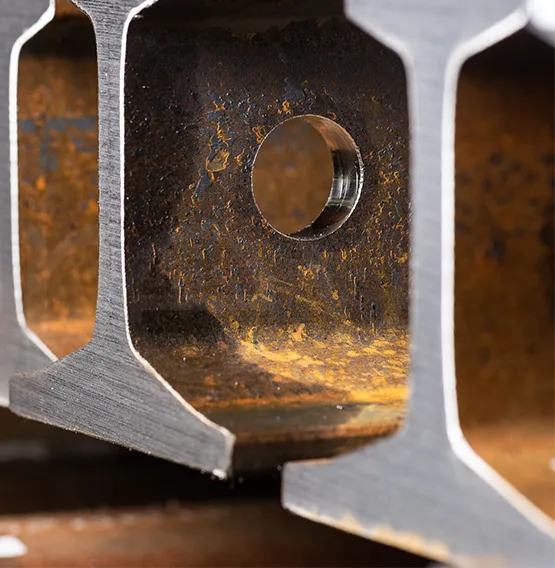
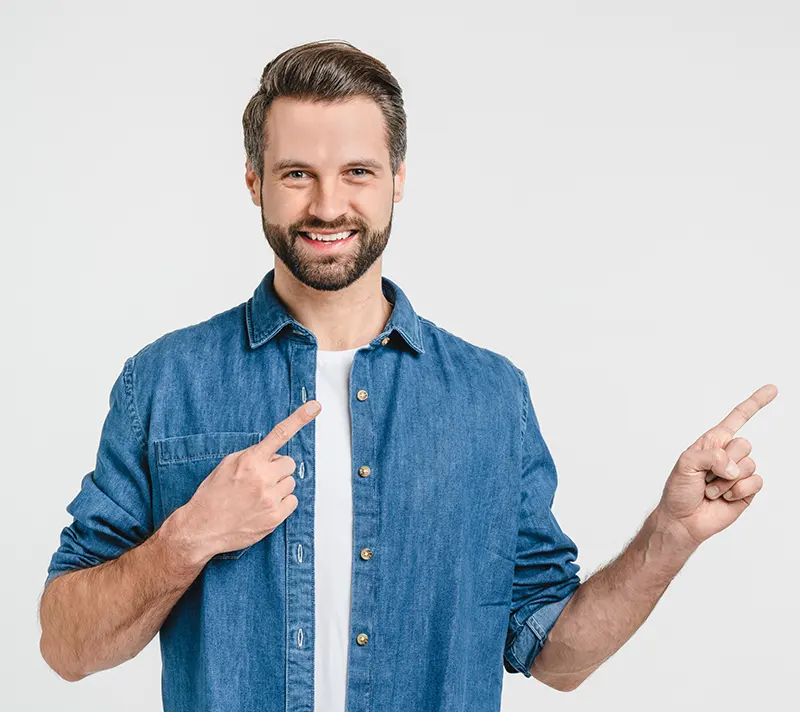